Your Trusted PCB Manufacturing Expert

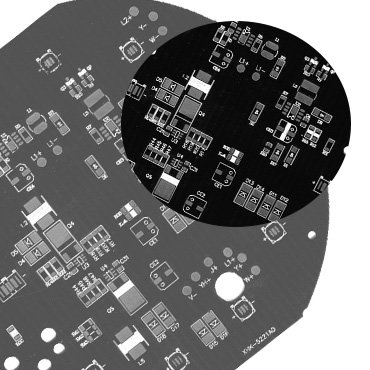


As a Printed Circuit Board provider, we offer a wide range of rigid circuit board materials to suit various applications, including paper-based PCBs, epoxy resin-based PCBs, aluminum-based PCBs, copper-based PCBs, ceramic-based PCBs, and more. Our experienced team can help you choose the most appropriate material based on the specific requirements of your product’s structure and characteristics.
At TORTAI Technologies, we understand that prompt delivery and high-quality products are crucial for getting your products to market quickly and successfully. That’s why we’re committed to providing exceptional customer service and ensuring that our products meet or exceed your expectations. Whether you need a prototype or high-volume production, we have the expertise and resources to deliver a reliable and cost-effective solution that meets your unique needs.
Guide to Choosing the Right PCB Substrate Material for Various Applications
As a PCB manufacturer, it is crucial to choose the right substrate material for your project. There are various types of base materials with different properties available in the market. In this article, we will guide you on selecting the appropriate PCB substrate material by considering its thermal performance, electrical characteristics, chemical properties, and mechanical properties.
The following are the four essential properties of dielectric materials:
1、Thermal Performance:
- Glass Transition Temperature (Tg): The temperature at which the substrate transitions from rigid to soft.
- Decomposition Temperature (Td): The temperature at which the material breaks down and loses its properties irreversibly.
- Coefficient of Thermal Expansion (CTE): The rate at which the material expands or contracts with temperature change.
- Thermal Conductivity: The ability of the material to transfer heat.
2、Electrical Characteristics:
- Dielectric Constant (Dk or Er): The measure of a material’s ability to store electrical energy.
- Dissipation Factor or Tangent of Dielectric Loss Angle (Tanδ): The measure of the power lost in a material.
- Volume Resistivity: The resistance of the material to the flow of charge.
- Surface Resistivity: The resistance of the surface of the material to the flow of charge.
- Electromotive Force: The ability of the material to resist electrical breakdown.
Chemical Properties:
- Flammability Specification (UL94): The resistance of the material to combustion.
- Hygroscopicity: The ability of the material to absorb water.
- Dichloromethane Resistance: The resistance of the material to chemical absorption.
Mechanical Properties:
- Peeling Strength: The bonding strength between the dielectric material and the copper conductor.
- Flexibility: The ability of the material to withstand mechanical stress without breaking.
- Young’s Modulus: The measure of the material’s resistance to deformation under stress.
- Density: The mass per unit volume of the material.
- Delamination Time: The time that the material can resist layering.
In addition to the properties of the substrate, you need to consider some important properties of the substrate. Here are some important features:
PCB Material | Typical use | DK | Tg (elC) | Recommend |
---|---|---|---|---|
FR-4 | Base Material, Laminate | 4.2 to 4.8 | 135 | Standardization |
CEM-1 | Base Material, Laminate | 4.5 to 5.4 | 150-210 | High-Density |
RF-35 | Bottom Layer | 3.5 | 130 | High-Density |
Teflon | Laminate | 2.5 to 2.8 | 160 | Microwave, HV, HF |
Polyimide | Bottom Layer | 3.8 | > = 250 | HV, Microwave, HF |
PTFE | Bottom Layer | 2.1 | 240 to 280 | Microwave, HV, HF |
Besides, it is also important to consider the type of PCB substrate material, which varies in thickness, strength, and design. Non-woven glass, braided glass, and Lleno are some popular types of PCB substrate with different dielectric constants and scattering factors.
To choose the right PCB substrate material, it is crucial to evaluate these properties and seek help from a qualified manufacturer engineering team. By considering these factors, you can select a high-quality substrate for your circuit board that meets your project requirements.
Misconceptions in Selecting PCB Substrate Material
As a professional manufacturer with years of experience in PCB design and manufacturing, I have observed several common misconceptions about selecting the appropriate material for PCBs. In this article, I will discuss some of these misconceptions and provide guidance on how to avoid them.
Misconception 1: Choosing Low-Cost Substrate Material Saves Money One of the most common misconceptions is that choosing low-cost substrate material will save money. While it may seem like a cost-effective option, using low-quality substrate material can lead to poor performance, reliability issues, and even complete failure of the PCB. Therefore, it’s essential to select high-quality substrate material that meets the specific requirements of your PCB application.
Misconception 2: High Dielectric Constant Is Always Better Another common misconception is that high dielectric constant (Dk) is always better. However, a high Dk value is not always beneficial and can sometimes cause signal degradation and loss. For high-frequency applications, it’s critical to choose a substrate material with low Dk values to minimize signal loss and ensure optimal performance.
Misconception 3: All Materials Have Similar Characteristics Some designers assume that all substrate materials have similar properties, which is another common misconception. Each substrate material type has unique characteristics that can significantly affect the performance and reliability of your PCB. Factors to consider when choosing substrate material include thermal conductivity, CTE, Tg, Dk, and others.
Misconception 4: Thicker Material Provides Better Performance Another mistake is that thicker substrate material automatically provides better performance. However, this is not always the case as thicker material can cause warpage, delamination, and other issues. The key is to select the correct thickness based on the specific requirements of your PCB application.
To avoid these misconceptions, it’s crucial to work with experienced manufacturers and suppliers who can help you select the appropriate substrate material for your PCB. They can provide expert guidance on choosing the appropriate material based on your specific requirements, ensuring reliability and optimal performance.
In conclusion, selecting the appropriate substrate material is crucial for designing efficient, reliable, and high-performance PCBs. By avoiding common misconceptions and working with experienced manufacturers, you can choose the right material that meets your unique needs and requirements.
Design Misconceptions of Rigid PCBs
As a professional PCB manufacturer, we have seen many common design misconceptions when it comes to hard printed circuit boards (PCBs). These misconceptions can lead to design errors that could affect the functionality and reliability of the final product. In this article, we will discuss some of the most common design errors made in the process of creating hard PCBs.
1、Insufficient Trace Width and Spacing
Many designers tend to overlook the importance of trace width and spacing, especially when they are working with high-speed signals. The width of a trace determines how much current it can carry, while the spacing between traces affects the level of interference or crosstalk. Therefore, it’s crucial to ensure that the trace widths and spacing meet the requirements for the intended application.
2、Inadequate Thermal Management
Thermal management is often neglected in PCB design despite being a crucial aspect that directly affects the performance and reliability of electronic devices. When designing hard PCBs, it’s important to consider the thermal conductivity of the materials used, as well as the placement of heat-generating components. Failing to address these aspects can result in overheating, which can cause the device to malfunction or even fail.
3、Neglecting the Importance of Ground Planes
Ground planes play a critical role in ensuring signal integrity, power distribution, and EMI/RFI reduction in PCB designs. However, some designers tend to overlook their importance, leading to poor signal quality and increased susceptibility to electromagnetic interference. It’s essential to allocate enough space for ground planes and ensure they are connected correctly to prevent any signal noise issues.
4、Overlooking EMC/EMI Considerations
Electromagnetic compatibility and electromagnetic interference considerations are essential when designing hard PCBs. They help to minimize the risk of interference from external sources or other circuits within the device itself. Ignoring these considerations can result in system malfunctions, signal loss, noise, or even damage to the device.
5、Limited Attention to Material Selection
Material selection is a crucial aspect of PCB design that affects its functionality and reliability. The choice of materials determines the physical properties of the PCB, including thermal conductivity, dielectric constant, and coefficient of thermal expansion. Therefore, it’s important to consider the intended application and choose materials that meet the required standards.
6、Inadequate Testing
Testing is an integral part of PCB design, and it’s essential to verify the design before moving to mass production. Insufficient testing can lead to errors that may not be detected until after the product release, leading to costly recalls and lost revenue. Therefore, it’s necessary to perform thorough testing at each stage of the design process, including prototyping, functional testing, and environmental testing.
Conclusion
Designing hard PCBs requires careful consideration of various factors, including trace width and spacing, thermal management, ground planes, EMC/EMI considerations, material selection, and testing. Neglecting any of these aspects can result in design errors that could affect the performance and reliability of the final product. As a professional PCB manufacturer, we advise designers to pay close attention to these aspects to ensure their designs operate correctly and reliably.